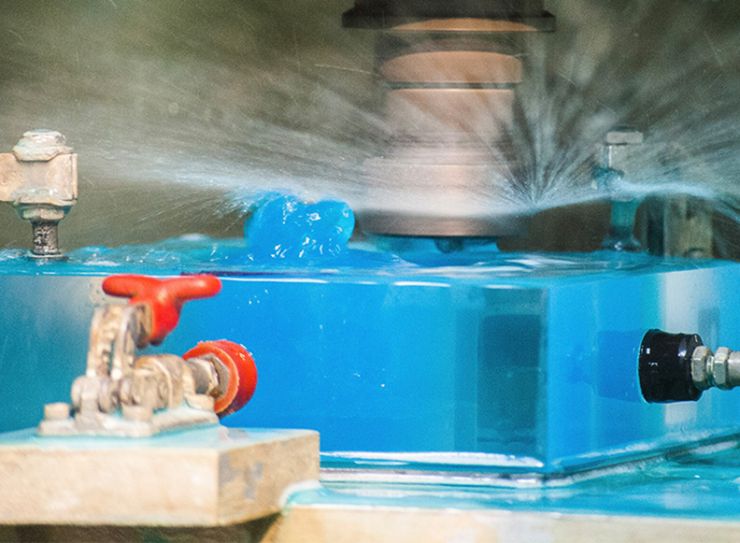
Glass Cutting
The introduction of materials into the Coresix glass fabrication process typically involves sizing of the substrate for subsequent operations. This can be achieved by several means, depending on the overall dimensions, thickness, and type of glass being used. In all cases, this initial operation is viewed by Coresix to be as critical as any other to assure the overall quality of the finished part. Though glass cutting is most often the beginning of our process, sometimes it’s the only process. If you need cut glass sheets, send us your requirements.
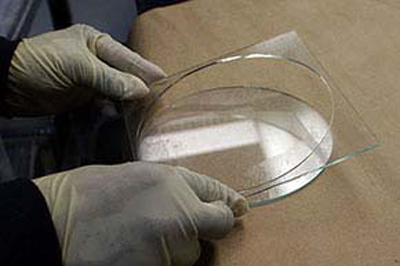
Scribe and Break
In working predominantly with flat sheet glass materials, mechanical scribe is the most common method of sizing glass substrate at Coresix. A series of precision CNC scribe tables accommodate large stock sheet glass purchased, whenever possible, directly from the manufacturer's production line. This assures a minimal amount of handling defects coming into our process. We then take careful measures throughout our scribing process to prevent the introduction of surface or edge defects.
LEARN MORE
Scribe and Break Process: Scribing is performed by rolling a small diamond wheel across the sheet to create a shallow “vent” in the glass surface. The accuracy and quality of this vent can affect the dimensional accuracy, edge quality, product strength and overall cleanliness of the finished product. The primary variables in achieving the best scribe include blade quality, wheel angle, scribe pressure, and cutting fluid. All of our machines are CNC programmable on two axis and are equipped with rotating cut heads providing accuracy on straight lines or radius to as tight as 25 microns.
Once the scribe is complete, our operators proceed to “break” the glass along the vent line. It is the experience and proficiency of the operator that further assures the quality of the edge through both breaking technique and monitoring of the scribe variables.
Coresix has a broad range in scribe and break capability with thickness from 50 microns to 15 millimeters. Sheet sizes up to 2300mm can be accommodated on our largest machines and finished parts down to 5mm can be scribed by our smallest machines. We specialize in the scribe and break production of both rectangular and shaped parts from micro sheet glass – including ultra-thing Willow Glass from Corning.
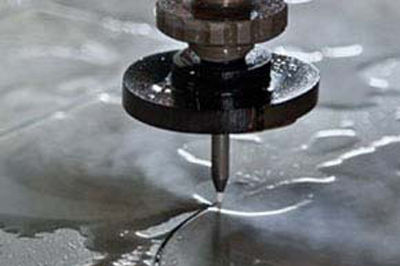
Water Jet
Though used at various stages of production for unique and creative applications, the water jet is also often used in the initial sizing of materials which are not conducive to the traditional scribe and break glass cutting process.
LEARN MORE
Water Jet Glass Cutting: Coresix is an experienced custom glass manufacture and glass cutting company.
Though used at various stages of production for unique and creative applications that require custom glass cutting, our water jet glass cutting machine is also often used in the initial sizing of materials which are not conducive to the traditional scribe and break process.
This generally includes custom glass products which are either too thick, limited in size (minimal edge trim) or prohibited by shape.
Water Jet Glass Cutting Process: The CNC waterjet glass cutting machine uses a powerful stream of water combined with a cutting medium or slurry to penetrate the material and custom cut glass shapes. Because this method cuts entirely through the thickness of the glass, special fixturing is used to support the finished substrate.
Our water jet is fully CNC programmable and capable of cutting nearly any shape while holding a positioning accuracy of 25-50 microns. When waterjet cutting glass, we typically cut glass from 1mm to several inches in thickness. For additional accuracy and substrate positioning capability, we have fitted the cutting head with a CCD camera device.
Call us today to find out how we provide world-leading glass fabrication for tomorrow's technologies.
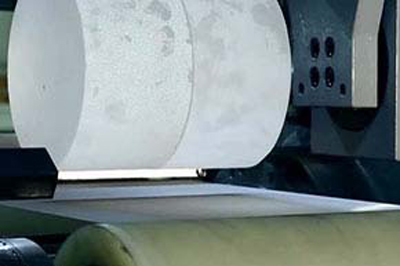
Wire Saw
For bulk materials including Fused Silica, BK7 and other Optical Glasses, our process starts with the wire saw. Providing very tight thickness and parallelism, the wire saw creates an ideal condition from which to perform the highest levels of finishing.
LEARN MORE
Wire Saw Process: The glass is cut by running a continuous strand of diamond coated wire from one spool to another. The wire is fed through a series of spacers which define the thickness of the slice. With the wire saw, we are able to process block materials as well as thick sheets, ingots and other formats, to as thin as .55mm. This allows us, in some cases, to salvage multiple parts from a thick substrate where a traditional grinding operation will yield only one.