
Custom Glass Components
Coresix Precision Glass has the variety of processes and depth of experience to make your vision reality. A creative and experienced engineering staff makes use of advanced process capabilities to design a solution to the most challenging needs. From in-house tooling to process design to full production, let us help with your custom glass requirements.
PROCESS
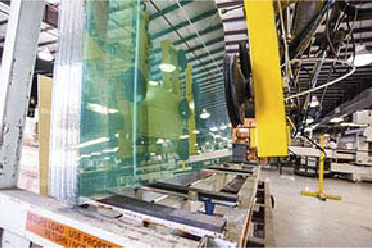
Substrate
Though we can achieve almost any format from standard sheet glass, custom components often require specialty glass materials like Fused Silica, BK7, and other Optical Glass. These materials can take the form of Blocks, Pressings, Cores, or Plates and require additional steps to create a suitable substrate for further processing. At Coresix, we have the tools and experience to convert any format of raw material into a finished component of your specifications.
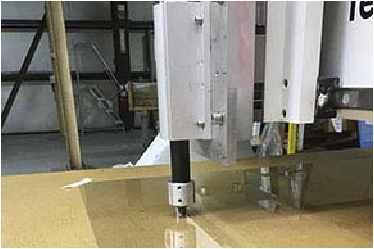
Cutting
For standard sheet glass materials, Coresix has a range of Precision Mechanical Scribe tables to meet most size requirements. Bulk materials are converted to appropriate blanks and, if necessary, can be further cut using the scribe process or Water Jet for intricate shapes. Often, processing (including lapping, polishing, optical coating, etc.) is more cost-effectively performed on a larger part, which can then be cut and formed to the final dimensions.
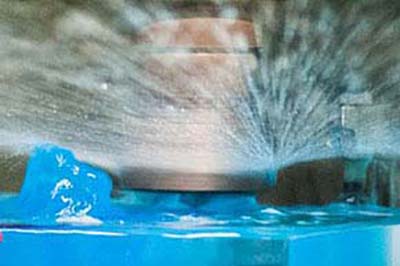
Edging
Though CNC Edging is available within certain size limits, a more cost-effective approach for small parts is to Hand Seam edges and corners on a diamond grinding wheel. This is a very consistent process that eliminated the sharp edge and corners making the parts safe to handle and promoting cleanliness through reduced particle migration.
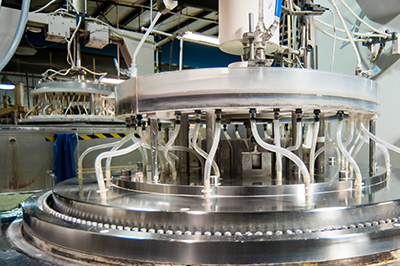
Lapping
Custom components will often require custom thickness or other characteristics (flatness, parallelism, etc) not available in standard material formats. Coresix maintains a variety of Single-Side Lapping and Double-Side Lapping processes with sufficient capacity to produce parts to your unique specifications in any quantities.
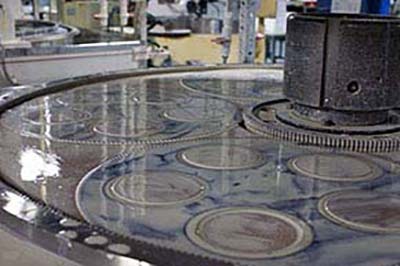
Polishing
Once lapped to thickness (and other requirements), whether as a substrate or in finished format, the surface and subsurface damage must be removed to bring the glass back to a clear state. We have an array of Double-Side Polishing processes to create surfaces from optically clear to ultra-low defects. We also offer Super Polish to achieve a smooth surface as low as 2A RMS.
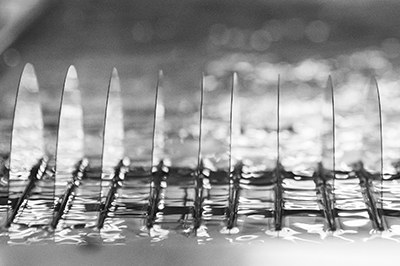
Cleaning
Our in-house tooling department can create custom carriers to enable Ultrasonic Cleaning of nearly any format parts up to 500mm square. We have multiple cleaning lines feeding directly into a Class 100 Optical Clean Room, where parts can be inspected under the most stringent conditions and packed to maintain cleanliness all the way to your door.
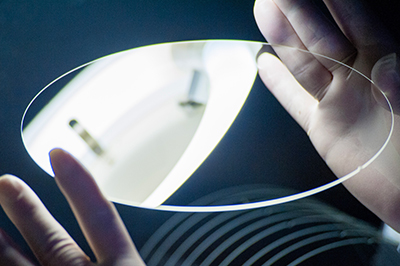
Inspection
Within our Class 100 Optical Clean Room, our most advanced inspection practices can be applied to nearly any part format. While metrology (Thickness, Parallelism, Flatness, Roughness, etc.) is often performed at the substrate level, a variety of lighting conditions are employed to inspect each part visually, assuring surface quality and cleanliness requirements are met 100% of the time.

SPECIFICATION
Dimensional Specifications
Most dimensions are limits under optimal conditions and are subject to evaluation upon inquiry.
Attribute | Minimum | Maximun | Tolerance |
---|---|---|---|
Thickness | 50µm | 10mm | +/- 2µm |
Dimensions (Scribed Edge) | 5.0mm x 5.0mm | n/a | +/- 50µm |
Dimensions (Hand Seam) | 12mm x 12mm | n/a | +/- 50µm |
Dimensions (CNC Edge) | 35mm x 35mm | n/a | +/- 25µm |
Dimensions (Scribed Edge) | 6.0mm | n/a | /- 100µm |
Diameter (CNC Edge) | 25.0mm | 450.0mm | +/- 25µm |
Feature Positioning | n/a | n/a | +/- 25µm |
Thickness Variation (TTV) | <1µm | n/a | n/a |
Flatness | 1/10 Wave/Inch | n/a | +/- 25µm |
Surface Roughness (RMS) | <2Å | n/a | n/a |
Scratch and Dig | 5/2 | n/a | n/a |
Particle Size | <5µm | n/a | n/a |
Bow/Warp | <10µm | n/a | n/a |
Actual specifications will be dependent upon material, format, and other factors. We will be glad to evaluate your requirements and advise the best possible process available.
CAPABILITIES
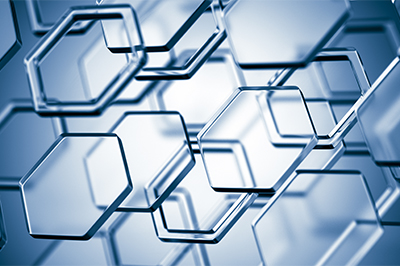
Dimensional
Coresix has an array of processes to achieve the tightest dimensional tolerances on custom shapes and components. Our CNC grinding stations have multiple tool change capabilities, enabling low relative dimensional variation between edges and other features. We use optical CMMs and SPC to assure dimensional specifications. In most cases, we can achieve tolerances as low as 25um.
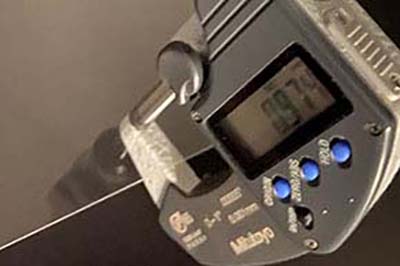
Thickness
Our in-house carrier and tool-making ability enable flexibility and creativity in the types of custom parts we are able to lap and polish. Running primarily 20” platforms, we can run most parts up to 450mm in dimension. Our advanced wafer processing capabilities apply to the most custom substrates, achieving thickness tolerances to +/-5um with thickness variation as low as 1um.
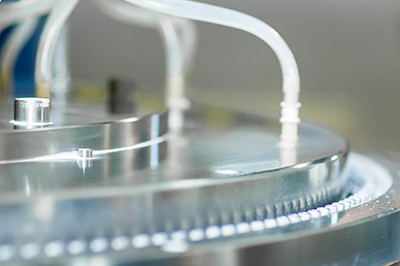
Flatness
Our ability to achieve extremely flat surfaces on a substrate prior to fabrication enables us to meet precision flatness requirements on the finished window format. As these flatness requirements can take many forms including TIR, TWE, RWE, Waves, and Fringes, we can help you determine exactly what specification is needed and design our process accordingly.
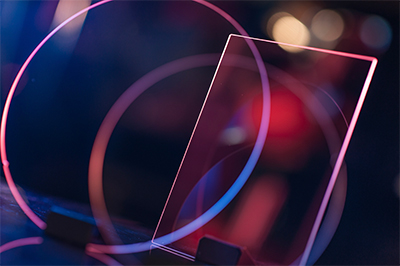
Parallelism
Like flatness requirements, through lapping and polishing processes, we can achieve the highest level of parallelism on a substrate from which we can then make the smaller components to sub-micron variation between surfaces virtually eliminating optical distortion through the glass.
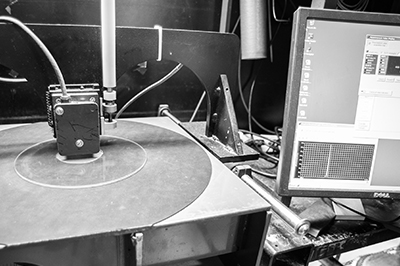
Roughness
Again, our substrate processing capabilities enable us to start the window fabrication process with the right material to assure your specifications will be met. Our standard substrate polishing process results in a surface roughness under 6A and our Super Polish process can create surfaces to 2A Ra.
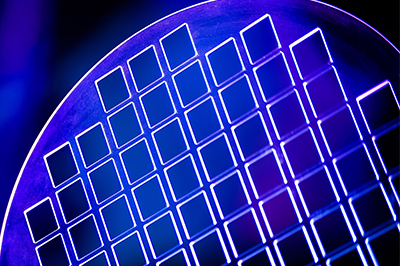
Cosmetic
Surface quality levels can be specified in many ways including the common “Scratch and Dig” standards, Maximum Defect Size, Light Condition (under which no visible defect is permissible), etc. Though polishing is often the final step in producing low defect wafers, it is the focus of our entire process to minimize defects through handling practices and process design. We regularly produce wafers to a 5/1 scratch and dig specification.
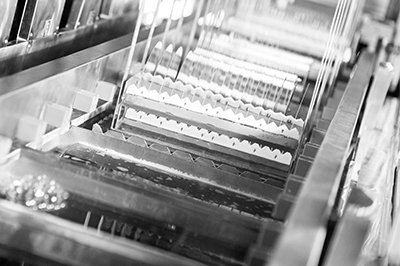
Cleanliness
With multiple ultrasonic cleaning lines feeding into a Class 100 Optical Clean Room and in-house tooling capabilities to make custom USW carriers, Coresix can produce the cleanest glass components in the industry. Employing a high-intensity light designed to enable the inspector to detect any level of cleanliness issue, we run a secondary inspection for residue and particulate. . In addition, we always work closely with our customers to assure what they are receiving exceeds their cleanliness expectations.
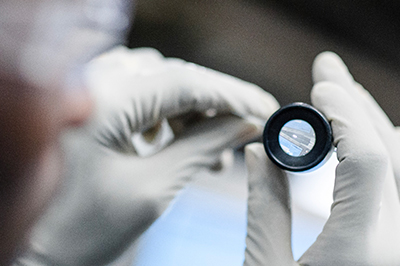
Inspection
With highly experienced operators in a Class 100 Optical Clean Room, Coresix can accurately and consistently verify the pristine surface conditions we create in our process. By using an appropriate light source, specifically calibrated for the surface condition to which we are inspecting, we can establish spec limitations to the highest standards and meet them reliably in high volume production.
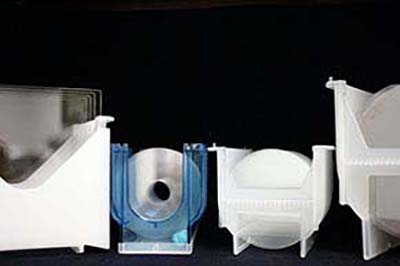
Packaging
Custom components often require a custom and creative packaging solution. From clean room tissue wrapping and packaging to custom-designed, non-contact alternatives, we consider the part specification, cleanliness requirements and unique customer needs to develop the most effective packaging option for custom components.