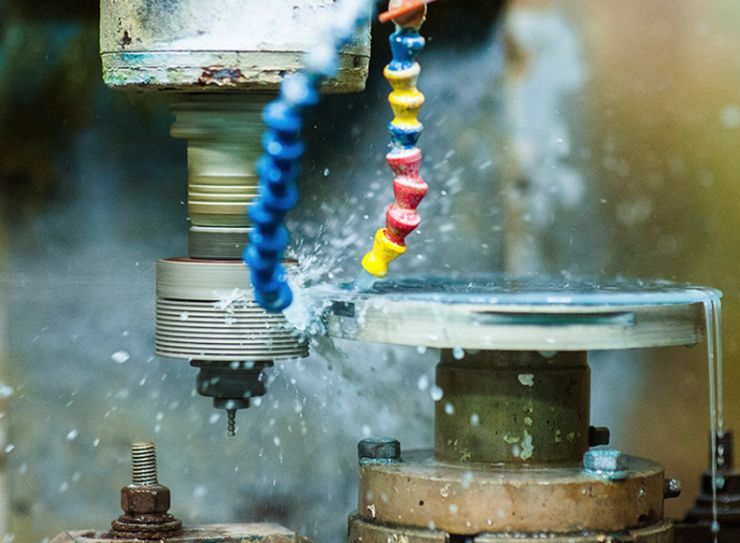
Glass Edging
Glass edging, whether by hand or CNC, is performed to remove the sharp, raw edge of a glass component. Proper edge treatment is critical to the overall performance of any glass substrate, affecting the safety of handling, protection from chipping, promotion of cleanliness, improved dimensional tolerance, and mechanical function. At Coresix, we have the capability to apply the correct edge for every application and the knowledge to provide the most efficient and cost-effective solution to your glass needs.
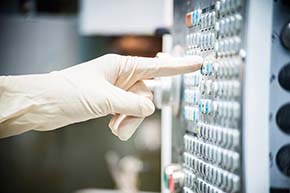
CNC Edging
At Coresix, we have the capability to apply the most effective edge for every application including 45°, radius, radius blend, and custom edge profiles. Each wafer is individually edged on a Precision CNC Edge Grinding Station. Where required, physical features are applied including Semi Standard Flats and Notches, alignment marks, cavities, and holes.
LEARN MORE
CNC Glass Edging: Our precision grinding stations are extremely versatile, offering a wide degree of flexibility in our process design. While the illustrations depict the most common edge and corner specifications, we can custom design and produce nearly any edge or corner profile to meet specific application requirements.
Our equipment is also capable of multiple tool changes within a single program, providing precision placement of features including notches, flats, holes, windows, pockets, etc. Whether running a multiple pass with a high-grit tool for an extremely fine edge finish, or performing a hand seaming operation to maximize cost savings, Coresix will engineer the edge that is right for your needs.
With CNC edge grinding stations, corners can be rounded to any preferred radius with a tolerance of +/- 0.20 mm. Radius corners offer the best protection against chipping and breakage due to the elimination of sharp points.
Edge Profiles: With CNC edge grinding stations, corners can be rounded to any preferred radius with a tolerance of +/- 0.20 mm. Radius corners offer the best protection against chipping and breakage due to the elimination of sharp points.
A typical 45° corner "cut" or "dub" can be applied by CNC edging or by hand edging operations (tolerance depends on operation). An optional 2x5 or other odd corner can be applied for orientation purpose.
NOTE: Edge Profiles illustrated with 3mm thickness and 1.5mm thickness for example only and can be applied to any thickness with some limitations below .5mm.
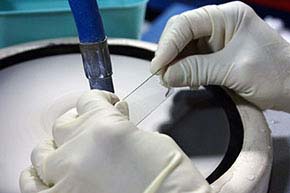
Hand Edging
Performed by an operator on a grinding wheel, this method is used primarily for small parts or for the economic application of noncritical edges.
LEARN MORE
Hand Edging: Performed by an operator on a grinding wheel, this method is used primarily for small parts or for economic application of noncritical edges.
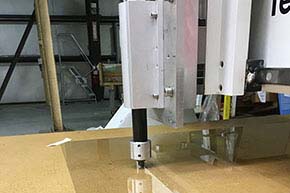
Mechanical Scribe
Whether the scribed edge is the final format, or an edge profile is to be added through hand seaming or CNC grinding, the scribe process is critical to the end result.
LEARN MORE
Mechanical Scribe: Our primary means of starting sheet glass into our process, our Mechanical Scribe methods have been honed to precision through many years of experience. For thin glass, the ultimate strength and flexibility is dependent upon a clean, defect free edge. From 100um to 10mm thick glass, our mechanical scribe process has been developed to a precise protocol of blade type, angle, pressure, scribe depth and speed to create the most pristine edge conditions possible.
Common Edging Terms
Bevel
Generally describes a well-defined size and angle to be ground on one or more edges. A bevel is usually specified for a cosmetic or functional purpose and requires a CNC or mechanical operation to achieve the required precision.
Ground or Milled Edge
Refers to the processing of the entire edge (usually all edges of the part) including top, bottom, and sidewall through a CNC or Mechanical operation.
Chamfer
Typically describes a uniform grind on the top and bottom of all edges with defined tolerances. Chamfers are most commonly applied with CNC grinding or other mechanical operation, though small components are "hand chamfered" on a grinding wheel.
Seam
Is usually used to describe a less critical edge treatment - often a "safety seam" or "edge break" with the primary purpose to remove sharp edges.